
Services
Customer Services
Introducing Infusent® – Powered by Baker Perkins
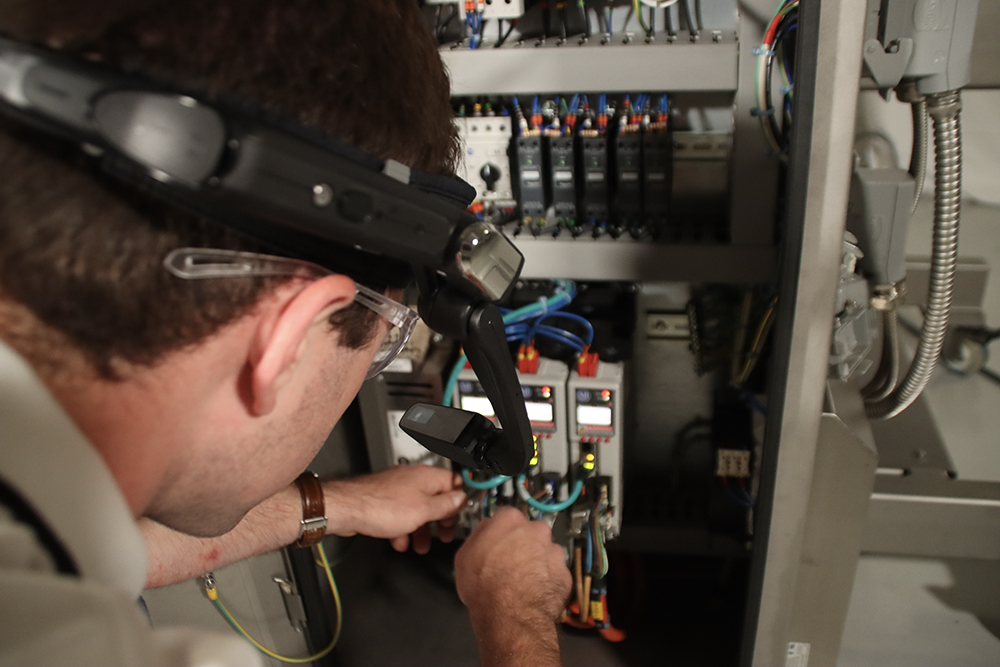
Infusent® is committed to maximizing customers’ return on investment on every machine we make. That is the focus of our Lifetime Support promise.
We ensure that the highest standards of service are available to customers as long as a machine remains in production anywhere in the world. That support extends beyond the customary supply of replacement parts and availability of engineers to maintain equipment and respond to breakdowns.
Rebuilds are available to return equipment to ‘as new’ levels of performance and when technology or your processes move on, we offer upgrades that improve capability beyond the original specification.
Process support enables customers to take advantage of changes in their market with new, innovative products. We provide operator training and offer service contracts that extend to responsibility for a complete line.
Lifetime Support keeps equipment running as effectively and reliably as when it was new, extends service life and improves performance.
Parts
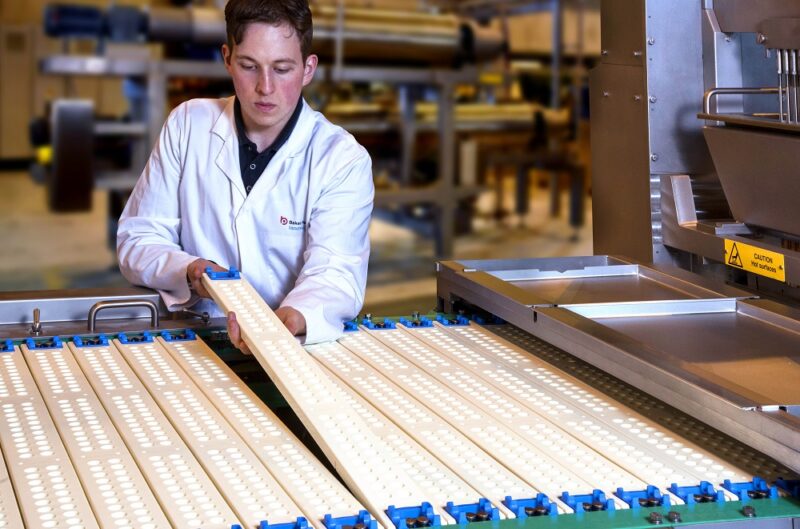
Genuine Baker Perkins parts are made to the original specification. They can be fitted without adjustment or modification and provide maximum performance and service life.
Expert advice is available from our team of product specialists. They use extensive technical records and consult our design and process technologists to identify the most appropriate original or upgraded part. The result is that the parts we supply always offer the best value for the money.
All Baker Perkins parts carry a 12-month warranty. They have the reassurance of full process and technical support from the Original Equipment Manufacturer.
Services + Support
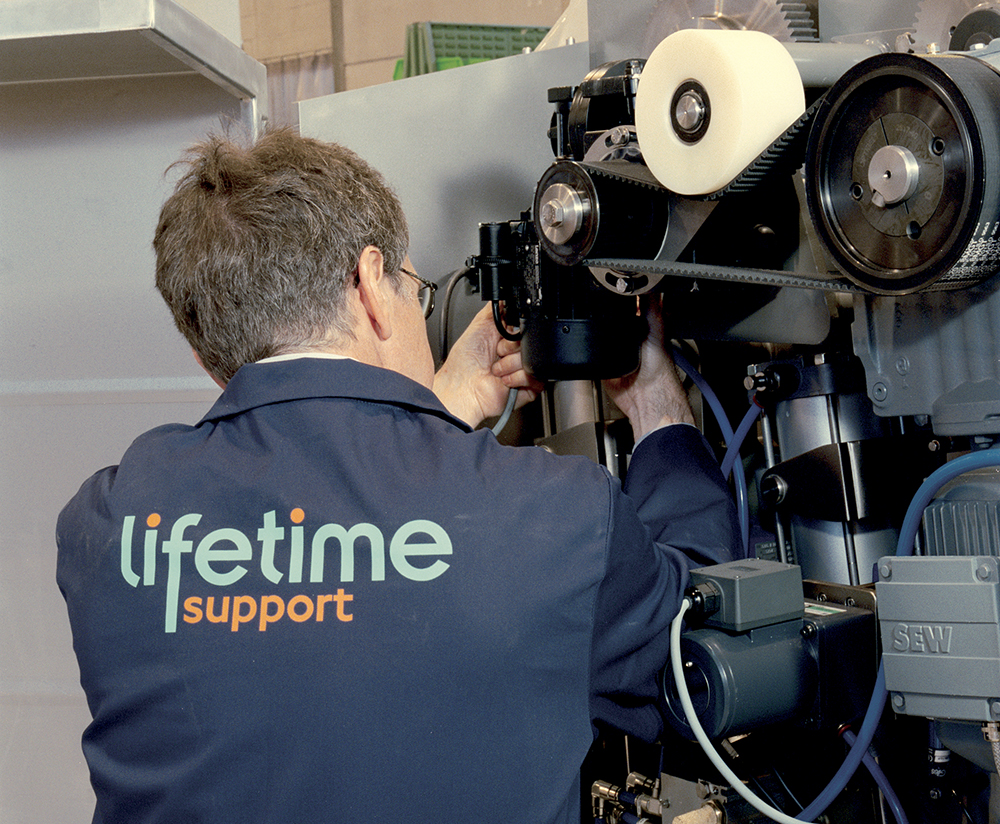
Disruption costs time, money and confidence. Because it’s our goal to make your processes work, we make it our number one objective to keep your equipment running smoothly, reliably and efficiently allowing you to keep advancing your business with confidence.
Complete Piece of Mind
Make the most of our customer support: we are here for your technical support, not just specific products. We offer advice and troubleshooting assistance in customized, full-service agreements that are tailored to your needs with special attention to individual services, spare part solutions or component offerings. We’ll be with you for the life of your machine or plant and beyond.
We ensure:
Your Availability
Your Efficiency
Your Profitability
Your Safety
Benefit from our Consultancy Expertise
Understanding your processes and your goals allows us to recommend appropriate actions and concepts for your needs. If necessary, our R&D engineers will get involved, too. Our support goes far beyond repairs. Be it minor adjustments or entire new developments, we have the expertise to optimize your processes. We can help you by looking ahead and spotting trouble before it happens.
Always There – Remote Support
Issue resolution does not always require an on-site presence. State-of-the-art technology and connectivity allow remote connection to PCs and mobile devices. Mixed-reality technology helps to get visual and audial feedback without even boarding a car or plane. It’s quicker and more cost-efficient.
Our remote support covers breakdowns, installation, inspection and monitoring, calibration, preventive maintenance, spare parts, technical training, testing, digitalization concepts, software updates, and technical information.
Connect Advisor
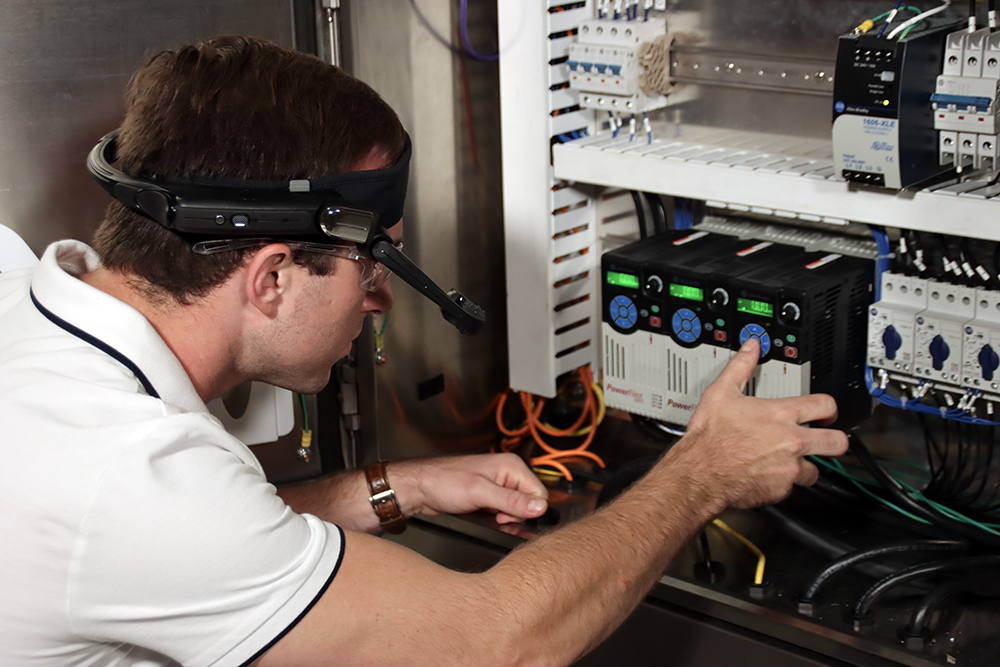
Inspections and maintenance account for up to a third of indirect costs in production plants. Yes, downtime is costly, annoying and… avoidable. With the right combination of condition monitoring and preventive maintenance you can save resources and time, preserve your reputation and staff morale, and make your business more sustainable. The key to optimization is knowing your processes in depth.
Enter Connect Advisor, our forward-looking digital solution enables you to become increasingly proactive, using analytics, diagnostics and more to optimize equipment life and productivity. We aim to help you optimize every aspect of your process solution. There is more to look forward to as we group all of our digital add-ons/services and controllers under the Connect platform in the future.
The features, benefits and access to experts which our existing customers have come to expect and rely on remain: integrated maintenance and support that combines guided digital workflows with real-time remote assistance from our experts. Customers transitioning to Connect Advisor can be rest assured that we will deliver the same high level of service they look for, in the best way for you.
Training
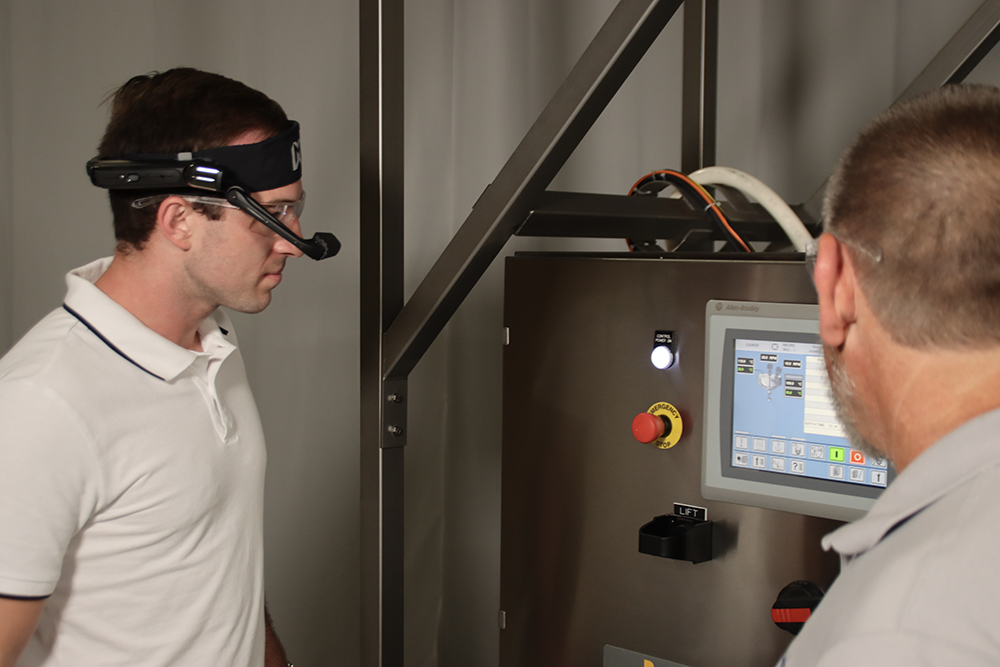
Training courses from Baker Perkins are the ideal way to develop the skills and knowledge your staff need to avoid waste and downtime and minimize running and ownership costs.
Courses are offered across the Baker Perkins process and equipment range in every sector. Each course is customized around the customers’ specific training needs and the equipment they work on.
The result is consistent peak performance of your plant or unit machines.
Meeting Business Objectives
We can develop courses that are directly relevant to your business objectives. Whether related to improving plant or unit machine performance or developing the skills of your employees, our training courses are designed around measurable outcomes.
.
Expert Tutors
The training is delivered by engineers with many years’ experience of working on Baker Perkins machinery in customers’ factories and who offer sound, practical advice to maximize the benefit from every course. Their unique understanding of both the equipment and the operating environment means that we are ideally positioned to provide training on all aspects of operation and maintenance.
Tailored Courses
Courses can be designed for anyone who works with or is in some way responsible for the correct operation and maintenance of Baker Perkins equipment. The content will be tailored to the needs identified by the customer. In addition to direct training, we can also provide ‘train-the-trainer’ courses. These enable companies to organize their own training courses as and when required to ensure that the benefits of OEM training are maintained.
Course Content
Courses typically include modules on:
- Process
- Equipment
- Control system architecture & philosophy
- Set-up and changeover of parts
- Normal operation
- Cleaning and hygiene
- Routine maintenance
- Fault finding and troubleshooting
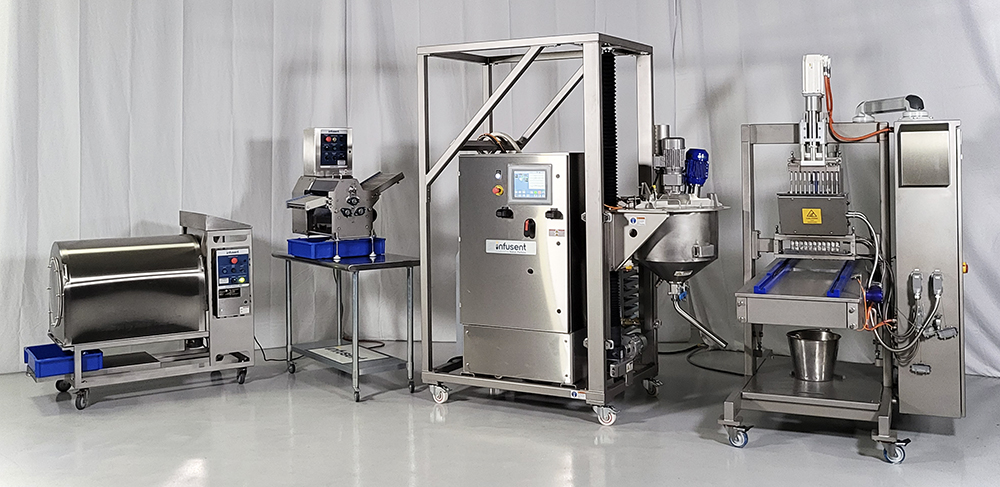
Process Support
Infusent™ provides full process support to customers in the infused products industry. We ensure they can take full advantage of the product and process benefits that differentiate depositing technology from conventional techniques.
Process support extends from advice and trials for establishing a new or upgraded product range before equipment is ordered to optimization of an installed system.
Innovation Center
Infusent™ pre-commissioning process support is based in the Innovation Center in Grand Rapids, Michigan. Here, equipment is available to enable customers to create new products and processes, produce samples for evaluation, and conduct feasibility trials.
The center is used by companies new to the confectionery industry, established manufacturers wanting to upgrade to depositing, and existing customers testing new product ideas without absorbing valuable production plant time. The Innovation Center is a secure environment where visitors are assured of total confidentiality.
Dedicated technology
The Innovation Center contains a wide range of pilot and laboratory-scale equipment. Experienced process technologists are on hand to offer help on product formulations, process parameters and equipment selection. A wide variety of ingredients, flavors and colors can be assessed.
Companies from every part of the world find that thorough trials, ideally using their own raw materials, provide a reliable basis for trouble-free commissioning of new plants or launching of new products.
Companies still using conventional technologies such as die forming use the Innovation Center to convert to the depositing process while maintaining the distinctive qualities of their product range.
Commissioning and training
Infusent™ installs and commissions new equipment and ensures product quality and output; operators can be trained either in the Grand Rapids Innovation Center or in the customers’ factory.
Ongoing services include benchmarking and process optimization of installed equipment. We analyze current operation, and fine-tune machinery to maximize performance and reduce operating costs.
Innovation + Solutions
+ Details
Infusent® builds hygienic, high-quality food manufacturing machines and safe, scalable solutions for infused edibles manufacturing.
Selflessness + Support
+ Details
Infusent® loves helping customers 24-7 as they grow, based on 120+ years of experience and lifetime support.
Loyalty + Leadership
+ Details
Infusent® exists to become the premier brand and market leader in food manufacturing equipment, building on 120+ years of solutions dedicated to helping companies innovate and grow.
People + Process
+ Details
People fuel the Process: Team Infusent® supports entrepreneurship for companies large and small, with expert engineering and manufacturing innovations for the traditional and medicated markets.
Experience + Expertise
+ Details
Infusent® builds on a 120+ year legacy of engineering solutions that help infused edibles companies create exceptional products efficiently, safely, and deliciously.
Innovation + Service
The Infusent® Innovation Center offers customers the equipment, facilities, and in-house expertise to develop new products and processes, produce samples for test marketing, and conduct feasibility trials. Test Products using our unique starch-free method:
- Hard candy in solid, striped, layered, and filled varieties
- Soft confectionery such as toffee, caramel, and fondant
- Gummies and jellies.
Interested in starting or scaling your infused edibles program today?
Contact An ExpertEND-TO-END SOLUTIONS
"What industry leaders have to say:"
Address
3223 Kraft Ave SE, Grand Rapids, MI 49512
Phone
(616) 784-3111